HISTORY
Bixby International Corporation was founded in Haverhill, Massachusetts in 1874 by brothers William E. and George H. (Bixby) to service the footwear industry in the Merrimack Valley of Eastern Massachusetts. The company concentrated on cut fiberboard, felt components and tacks utilized in the assembly of footwear. Bixby expanded its services to this growing industry to become the dominant supplier nationwide in its product specialties for many decades.
During the 1950s, under the leadership of second and third generation descendants of the founders, the company expanded to overseas markets, including Europe, South Africa, Australia, New Zealand, Japan, Canada, and Central and South America. Product lines were expanded to include the stiffening and shape retention components used in the toe and heel areas of the footwear. It was during this period that product development became an integral factor in the company’s progress. The company’s specialty products were recognized as being on the leading edge of shoe technology, and the name “Bixby” became well known in footwear producing centers throughout the world.
During the 1960s, Bixby began a vertical integration program, becoming its own supplier of profile extruded, and bulk hot melt adhesive products. By 1969, 20 percent of the company’s product needs were produced internally and by 1972, Bixby’s production facilities provided 98 percent of the company’s product requirements. This production capability included not only traditional fabric saturation/coating capabilities, but also production techniques never previously utilized for footwear applications, including high-performance, multi-operation sheet extrusion lines.
In the mid-1980s, seeking new opportunities for growth, Bixby concentrated its product development and marketing effort on expanding and accelerating its product/market diversification program. The company’s strategy was to focus on markets where Bixby’s unique production capabilities could provide significant
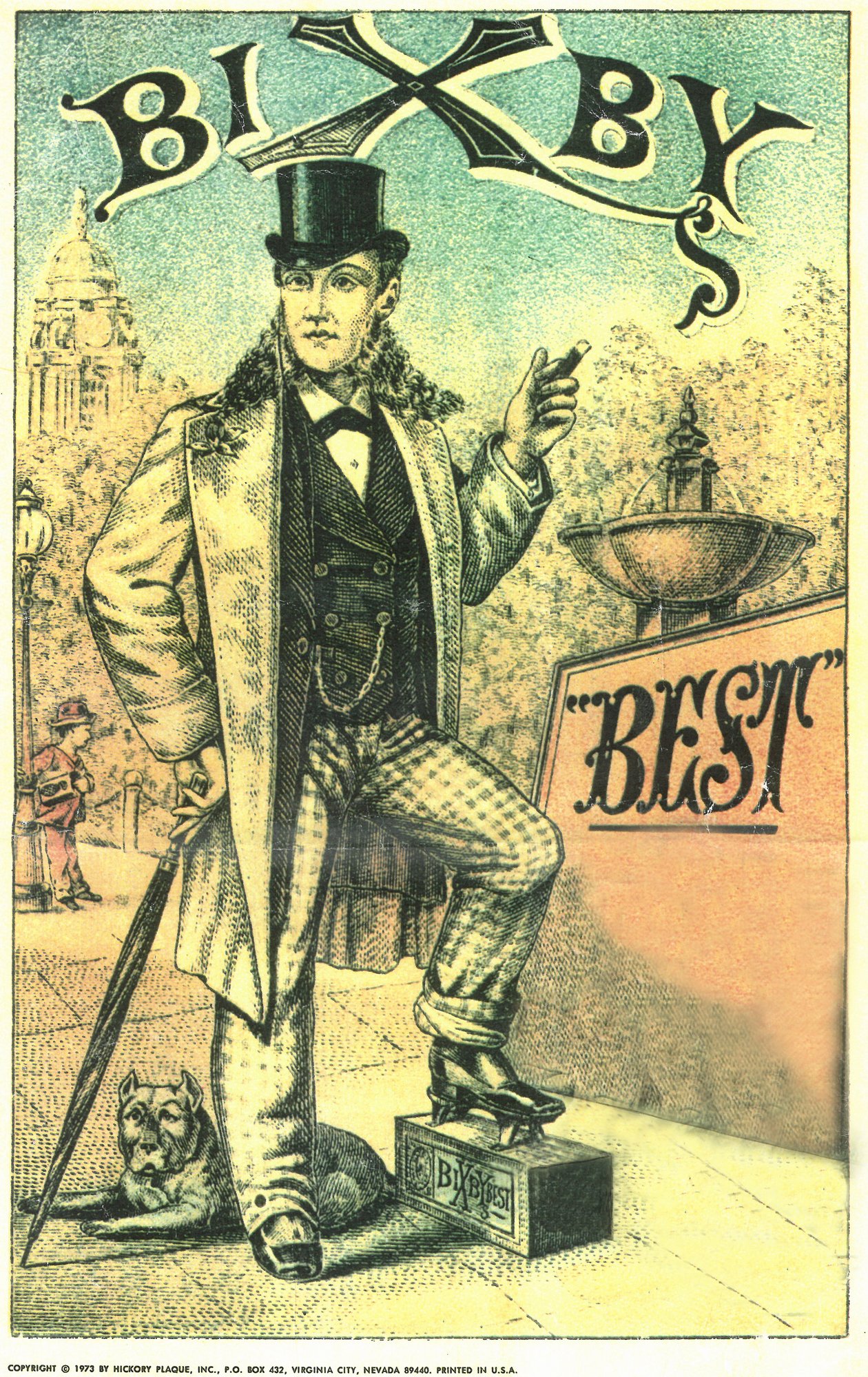
competitive advantages and where the company’s product development and marketing capabilities could ensure rapid penetration of these markets. The operations moved from several older factory buildings located along the Merrimack River in Newburyport, into our current larger 100,000-square-foot modern production facility, which is only a few miles away from the river in the Lord Timothy Dexter Industrial Park, also in Newburyport, Massachusetts.
Bixby succeeded in diversifying its business into broader industrial applications which required it to expand its capabilities and capacity through the 1990s. In 1993 Bixby designed and installed a unique 72" wide line comprised of two large extruders and associated roll stacks, including robust upstream and downstream web handling capability. This innovative processing line allowed flexibility to make multi-layer structures consisting of two different extruded polymers in combination with up to three different roll substrates like fabrics, foams, or films in a single pass. Applications grew in more sophisticated end-use markets like recreation, building and construction, industrial belting, and coated and reinforced fabrics, among others requiring multi-layer solutions.
Bixby entered the new millennium with positive momentum and a need to support a diverse and growing customer base in rapid product development and prototyping. A laboratory pilot line was designed and installed to mirror the capabilities of the big production lines but on a small scale. This development line and its skilled staff allow Bixby to work rapidly, intelligently, and cost-effectively with our customers on concepts we seek to commercialize together. The pilot line is the backbone of our research and development activities and is complemented by a fully staffed group of engineers and materials specialists. Our testing lab, which sits beside our pilot line, is equipped with instruments and equipment that help us create and validate complex thermoplastic composite structures during development and after commercialization.
In 2005, Bixby upgraded its two original extrusion lines to add flexibility and improve quality and consistency of products produced there. These production lines have the capability in one case to make up to three extruded layers combined with various substrates, and in the other to handle up to three different substrates and combine them with an extruded web. Five years later the newest 72" line received another upgrade to further increase its flexibility and capability to run both extruders in tandem as designed, or to run separate mono- or bi-layer extrusions in opposite directions. This upgrade increased available capacity for wide products and effectively added another process line on the floor. A year later a sophisticated slitter/winder was added in-line. This in-line web converting installation coupled direct to a production extrusion line is the first of its kind.
Over the last decade, in addition to continuously investing in and improving its production operations to consistently supply technically advanced mono- and multi-layer polymer sheet solutions, Bixby has focused on being an environmentally conscious and sustainable manufacturing operation. Seeking to minimize its environmental impact, Bixby has invested in renewable energy with the installation of a 50-kilowatt solar array. Shortly thereafter, a new, more efficient chilled water system was added which does not depend solely on high-energy refrigeration and cooling systems; but instead takes advantage of the cooler climes so often experienced in New England. Additionally, decades old energy intensive lighting systems were replaced and upgraded with modern, energy efficient lighting throughout the plant and office areas.
With these capabilities, and our skilled and motivated staff, we have been able to invest in and grow our innovative business model to supply customers with best-in-class custom plastic extrusion solutions.
Expanding from the footwear applications of over 140 years ago, to the many industrial applications developed in the last quarter century, we continue to deliver new technical solutions to major corporations around the globe in industries such as medical, orthopedic, military, recreational, renewable energy, aerospace, and transportation.